時(shí)間: 2025-03-03 09:13:21
來源: UCT
點(diǎn)擊率: 10 次
摘要:近年來,冷噴涂工藝越來越多地用于金屬部件的增材制造,被稱為冷噴涂增材制造 (CSAM)。與基于熔融的增材制造工藝不同,CSAM 是在固態(tài)下實(shí)現(xiàn)的,具有一些優(yōu)勢(shì),例如不存在嚴(yán)重的氧化或相組成變化。目前,CSAM 的主要限制是噴涂態(tài)沉積物普遍較低的延展性。在本文中,我們以銅作為模型材料,展示了一種克服這一限制的方法。重要的是,在不犧牲機(jī)械強(qiáng)度的情況下,實(shí)現(xiàn)了噴涂態(tài)沉積物的高延展性。此外,我們表明,在沒有任何后熱處理的情況下,CSAM 銅的性能與塊狀非增材制造銅相當(dāng)。關(guān)鍵詞:冷噴涂;銅;高延展性;增材制造 近來,冷噴涂技術(shù) (CS) 正逐漸被認(rèn)為是 一種新型增材制造 (AM) 技術(shù)。在冷噴涂工藝中, 微米級(jí)的粉末顆粒在推進(jìn)氣體的作用下加速, 推進(jìn)氣體通過拉瓦爾噴嘴供給。然后,顆粒以超音速撞擊到芯軸/基材上,并發(fā)生廣泛的塑性變形,與底層材料形成牢固的結(jié)合 [1–3]。冷噴涂具有生產(chǎn)時(shí)間短、工藝經(jīng)濟(jì)性好、幾乎無限的零件尺寸能力以及局部沉積的靈活性。鑒于這些,CS工藝實(shí)際上提供了獨(dú)特的優(yōu)勢(shì)與增材制造技術(shù)相比,熱能是 主要的沉積原理(選擇性激光熔化、電子束熔化、激光工程凈成形和激光金屬沉積)[4,5]。此外,由于CSAM是在固態(tài)下完成的,因此金屬零件的生產(chǎn)沒有嚴(yán)重的氧化或相變 [6, 7],重要的是,CS 更適合于高反射率金屬(如銅)的增材制造,而這些金屬 使用激光輔助增材制造工藝處理時(shí)存在問題 [8]。
冷噴涂工藝現(xiàn)在是一種成熟的技術(shù), 用于各個(gè)行業(yè)的金屬沉積。它已被用于生產(chǎn)保護(hù)性 或性能增強(qiáng)涂層,以及接近*終形狀的零件 [9]。除此之外,CS 也已被證明是一種經(jīng)濟(jì)高效的工藝,用于修復(fù)和恢復(fù)損壞的航空航天部件(在 [10] 中,修復(fù)使用CS修復(fù)海鷹直升機(jī)模塊的案例,從而節(jié)省了高達(dá)新組件制造成本的 35-50%)。 目前,冷噴涂工藝的主要限制是沉積物極低的延展性,這是由于粉末顆粒的嚴(yán)重塑性變形以及相關(guān)的冷作硬化現(xiàn)象引起的。為了恢復(fù)延展性,CSAM 材料 通常要經(jīng)過熱處理以誘導(dǎo)再結(jié)晶 和固結(jié) [11]。這種在噴涂態(tài)下具有高機(jī)械強(qiáng)度但幾乎為零的延展性,以及通過后熱處理提高延展性的方法,已被多位研究人員報(bào)道。例如,Meng 等人 [12] 觀察到冷噴涂304不銹鋼的延伸率低于1%,經(jīng)過熱處理后提高了5倍。對(duì)于 Inconel 718,觀察到噴涂態(tài)材料的延伸率僅為0.5%,退火后增加了8-10倍[13–15]。Yu 等人(2019) 也觀察到Cu 具有高機(jī)械強(qiáng)度和較差的延展性,幾乎沒有延伸率,經(jīng)過熱處理后,延展性再次得到改善 [16]。Yin 等人 (2018) 報(bào)道,冷噴涂Cu在噴涂態(tài)下的延伸率約為 2.5%,在 500 °C 下退火 4 小時(shí)后提高了 7.6% [17]。 本研究展示了一種克服該問題的方法。我們的Cu沉積物在噴涂態(tài)下表現(xiàn)出高延展性,無需任何熱處理。重要的是,這在沒有 任何顯著的機(jī)械強(qiáng)度折衷的情況下實(shí)現(xiàn)的,并且使用更便宜的氮?dú)庾鳛楣に嚉怏w(不需要氦氣)。在本文中, 介紹了粉末粒度和工藝參數(shù)對(duì)微觀結(jié)構(gòu)和力學(xué)性能的影響,并將我們的 CSAM Cu 在噴涂態(tài)下的性能與塊狀 Cu 進(jìn)行了比較。
圖 1. 使用的 (a) 細(xì)銅粉和 (b) 粗銅粉的粒度分布。
表 1:沉積工藝參數(shù)
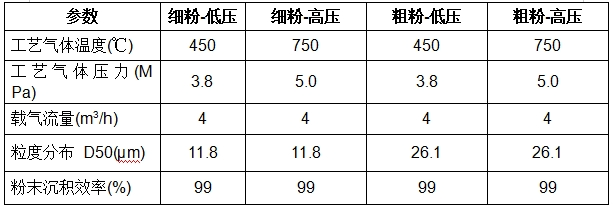
使用兩種具有不同粒度分布的高純度 Cu粉末(99.95%,Impact Innovations GmbH)來驗(yàn)證已發(fā)現(xiàn)的原理(圖 1)。霧化粉末具有球形形態(tài),圖 22 顯示了細(xì)粉的形貌,其 D10 = 6.2 μm,D50 = 11.8 μm,D90 = 17.8 μm,粗粉的 D10 = 18.9 μm,D50 = 26.1 μm,D90 = 40 μm。 為了幫助理解其基本原理, 通過 CSM EVOLUTION 冷噴涂儀(Tecnar Automation Inc.,加拿大)測量的飛行中粉末顆粒的速度,該設(shè)備配備了連續(xù)二極管激光源,用于照亮顆粒羽流(790 nm 波長, 3.3 W 功率,70 mrad 發(fā)散角)。 使用了具有中央噴射系統(tǒng)的ISS5/8高壓槍和OUT1噴嘴(膨脹比5 .6)進(jìn)行定位。氮?dú)庥米魍七M(jìn)劑和原料載體氣體。結(jié)合兩種原料粉末(細(xì)粉 、粗粉 )和兩組建議的工藝參數(shù)(低- 低壓 、高- 高壓 ,表1),準(zhǔn)備了四個(gè)樣本集。LP和HP的參數(shù)值是在初步的內(nèi)部研究中獲得的。對(duì)于所有四個(gè)沉積實(shí)驗(yàn),使用了500mm/s的槍速、30mm的距離和1mm的步長。沉積參數(shù)矩陣見表1。對(duì)于每組 ,使用尺寸為70×70mm2的兩塊鋁板作為基底沉積5-6mm厚的銅涂層 。沉積后,移除鋁板以獲得自由站立的銅涂層。未進(jìn)行額外的熱處理。為了幫助理解基本原理,使用配備連續(xù)二極管激光源的CSM進(jìn)化冷噴射儀(Tecnar Automation Inc.,加拿大)測量了粉體顆粒在飛行過程中的速度 ,以照亮顆粒羽流(波長790nm ,功率3.3W,發(fā)散角70mrad)。 使用標(biāo)準(zhǔn)程序從沉積物中制備金相樣品, 并使用1微米金剛石研磨膏進(jìn)行*終拋光。使用EVO MA分析樣品橫截面15掃描電子顯微鏡(Carl Zeiss,德國)。通過使用FEG/SEM Zeiss Ultra Plus(Carl Zeiss,德國)進(jìn)行高級(jí)電子背散射衍射 (EBSD) 映射,擴(kuò)展了微觀結(jié)構(gòu)分析,該設(shè)備配備了 HKL Nordlys EBSD 探測器(Oxford Instruments,英國)。EBSD 數(shù)據(jù)集是在 20 kV 的加速電壓下采集的,在高/電流模式下使用Aztech軟件(Oxford Instruments,英國)時(shí),孔徑為120微米。采集步長為200納米,相機(jī)合并經(jīng)過調(diào)整,以實(shí)現(xiàn)可靠的模式識(shí)別(在本例中為 4 × 4)。 樣品的致密性通過使用氦氣泄漏檢測器(Qualytest HTL 260,Pfeiffer Vacuum GmbH,Asslar,德國)在德國 Forschungszentrum Jülich 的 IEK-1 中進(jìn)行氣密性測試來評(píng)估。在沉積物的一側(cè)保持 He 的流動(dòng),同時(shí)在其另一側(cè)抽取真空。記錄通過樣品泄漏的 He 的量。 對(duì)于機(jī)械性能測試,選擇了拉伸測試和硬度測量。對(duì)于前者,從獨(dú)立式Cu 中電火花線切割出扁平試樣(長度為60毫米),并根據(jù) ENISO 6892–1 標(biāo)準(zhǔn)使用傳統(tǒng)拉伸試驗(yàn)機(jī)進(jìn)行測試,不同之處在于建議的機(jī)械引伸計(jì)被虛擬數(shù)字圖像相關(guān) (DIC) 引伸計(jì)取代。此前已評(píng)估該裝置是進(jìn)行材料表征的有效方法 [18, 19],并且表明非接觸式引伸計(jì)產(chǎn)生的結(jié)果與機(jī)械引伸計(jì)獲得的結(jié)果完全相當(dāng)。使用虛擬引伸計(jì)的另一個(gè)優(yōu)點(diǎn)是,*大限度地減少了由于引伸計(jì)刀具刮擦樣品表面而導(dǎo)致裂紋萌生的可能性。以0.4毫米/分鐘的恒定速率施加拉伸載荷,直至斷裂,并記錄材料的應(yīng)力響應(yīng)。使用Q10A+(Qness,奧地利)通過維氏法測量沉積物的硬度。考慮到晶粒尺寸和微觀結(jié)構(gòu)特征,所有樣品均選擇300gf 的載荷 (HV0.3)。測量按照 ISO6507–1標(biāo)準(zhǔn)進(jìn)行(壓痕間距至少為壓痕尺寸的3倍)。使用20個(gè)壓痕來計(jì)算每個(gè)樣品的平均值。對(duì)于細(xì)粉和粗粉,使用雙尾非配對(duì)t檢驗(yàn)來確定在低壓 (LP) 和高壓 (HP) 下生產(chǎn)的沉積物的硬度之間的統(tǒng)計(jì)顯著性。使用的顯著性水平為 *p = 0.01。 樣品的熱conductivity λ值是根據(jù)熱擴(kuò)散系數(shù)a、密度P和比熱容cp的 測量結(jié)果,按照公式laλ=a×P×cp計(jì)算得出。熱擴(kuò)散系數(shù)的測量采用激 光閃蒸法,在真空條件下使用LFA 1000測試儀(德國林賽公司)進(jìn)行。為了確保吸收均勻,吸收為了使激光脈沖的吸收均勻且表面的輻射特性相等,將10x10x2mm3樣品涂上一層薄薄的石墨。對(duì)于所有樣品,在每個(gè)溫度下(從20到800 'C)進(jìn)行五次測量。樣品的密度p使用阿基米德方法(將樣品浸入水中)測量,其各自的溫度依賴性是基于純塊狀銅的密度-溫度依賴性計(jì)算的。對(duì)于計(jì)算,使用了純銅的熱容C。 將通過各種方法獲得的性能與塊狀銅材料進(jìn)行比較。為了避免混入潛在的第二影響并保持完全的相互可比性,Cu塊體是與用于霧化此處使用的兩種粉末相同的材料。
圖 2. 所用細(xì)銅粉和粗銅粉的球形形貌。
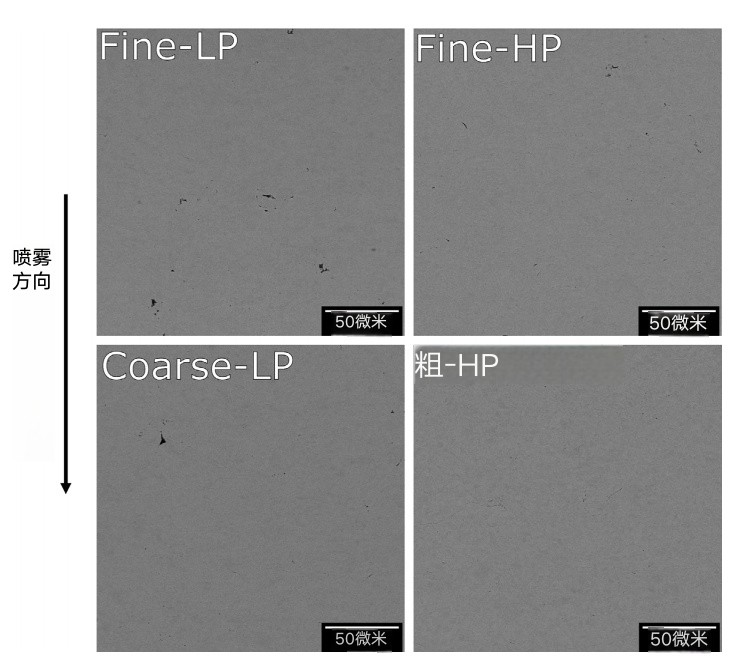
圖 3. 四種 CSAM 銅沉積物的致密微觀結(jié)構(gòu)。
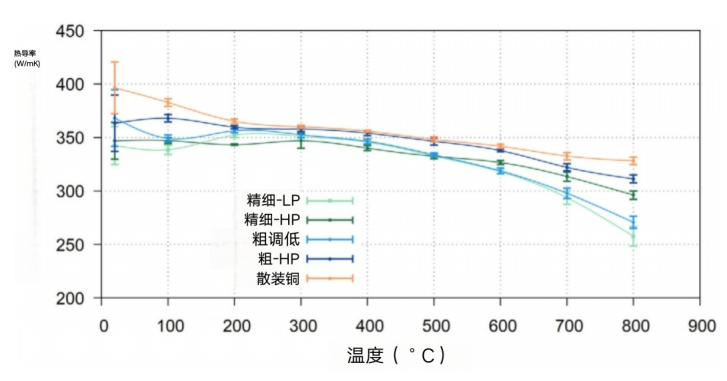
圖 4. 四種 CSAM 銅沉積物和塊狀銅的導(dǎo)熱率。
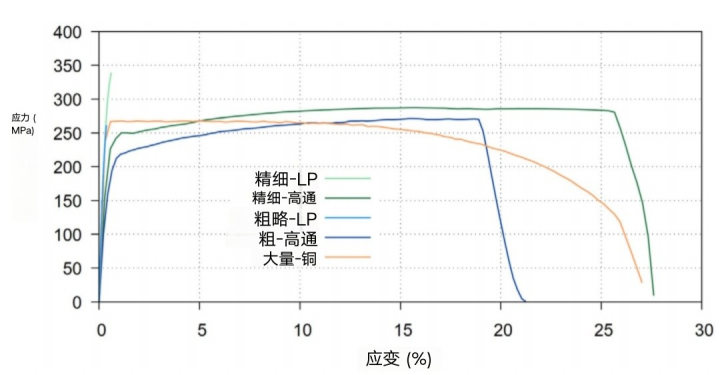
圖 5. 應(yīng)力-應(yīng)變曲線顯示了在高工藝參數(shù)下沉積的冷噴涂銅具有高強(qiáng)度和延展性,與塊狀銅的性能完全相當(dāng)。
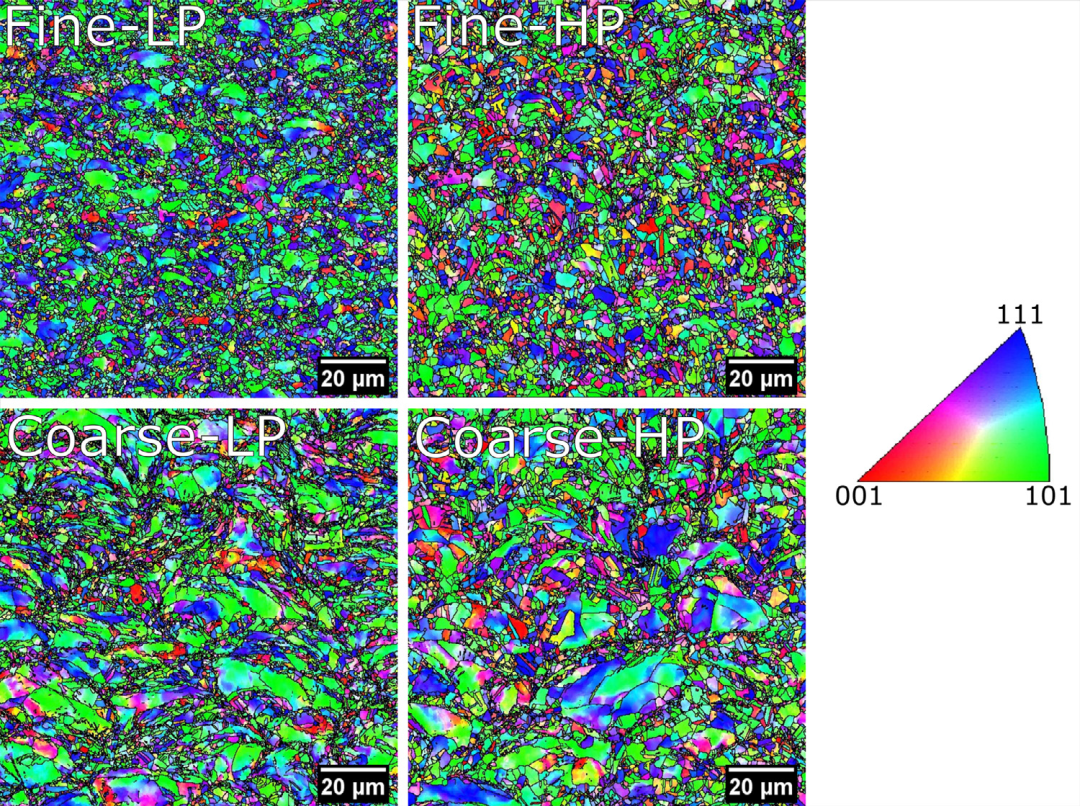
圖 6. 冷噴涂銅沉積物微觀結(jié)構(gòu)的EBSD IPF 圖,顯示雙峰晶粒分布。
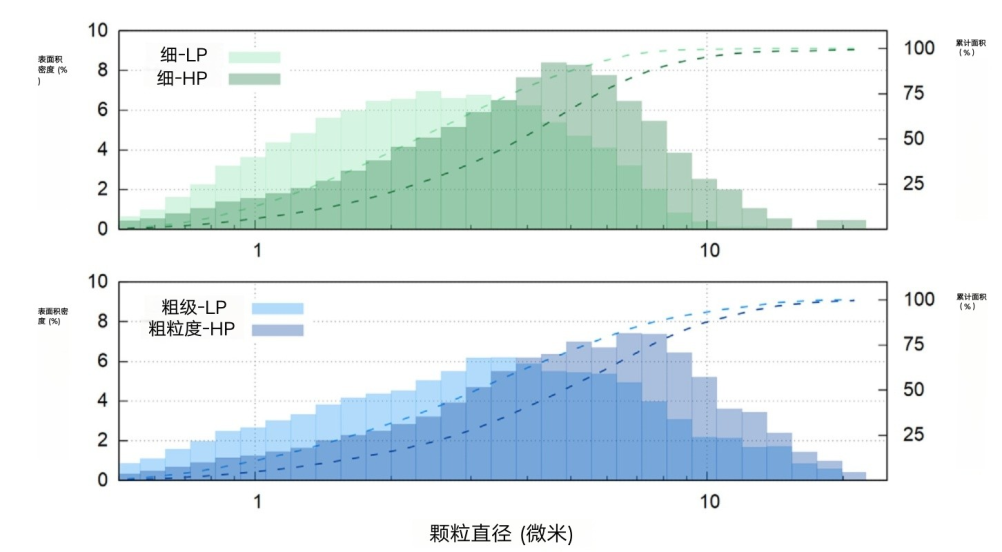
圖 7. CSAM Cu 沉積物中的面積晶粒尺寸分布。
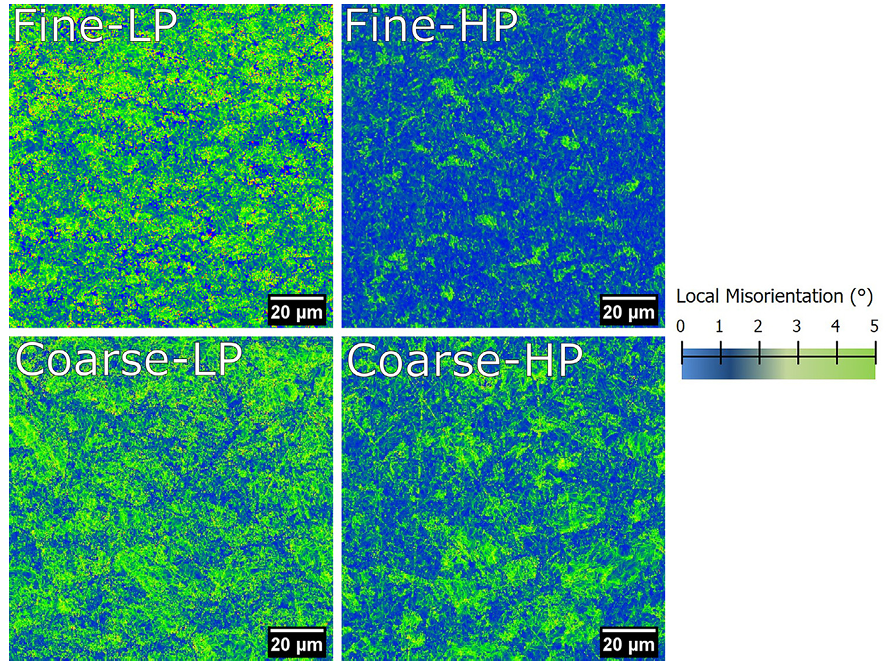
圖 8. 冷噴涂銅的局部晶粒取向差圖,顯示了局部塑性應(yīng)變的量。
圖33中的SEM BSE 顯微照片顯示,在低參數(shù)和高參數(shù)下,由兩種粉末沉積的材料都具有非常致密的微觀結(jié)構(gòu)。事實(shí)上,通過阿基米德浸沒法測定的Cu沉積物的密度(表 2)對(duì)應(yīng)于低于1.5%的孔隙率,即與塊狀冶金Cu相當(dāng)?shù)闹?。為了進(jìn)一步評(píng)估密度,使用 He 泄漏檢測對(duì)致密的Cu沉積物進(jìn)行了氣密性測試。在所有沉積物中,觀察到小于1×10?7mbar?l/s 的He流量。根據(jù) [20, 21],低于1 ×10?7mbar ?l/s 的值被認(rèn)為是非常密封的系統(tǒng)。換句話說,該測試證實(shí)了冷噴涂沉積物非常致密,并且Cu沉積物中有限的孔隙率不是相互連接的。 如果與其他增材制造工藝生產(chǎn)的銅進(jìn)行比較,所獲得的密度值會(huì)更加突出。例如,Lykov等人(2016 年)在通過選擇性激光熔化工藝生產(chǎn)的銅中實(shí)現(xiàn)了88.1% 的密度 [22],而 Kumar等人(2019 年)在通過粘結(jié)劑噴射增材制造生產(chǎn)的燒結(jié)和 HIP銅中測量了77% 到97% 的密度 [23]。 如圖 4 所示,記錄了Cu沉積物的導(dǎo)熱率,溫度范圍為20–800 °C??梢杂^察到,所有樣品的導(dǎo)熱率與塊狀Cu對(duì)應(yīng)物相當(dāng),間接證實(shí)了沉積物的質(zhì)量。略微更好的HP沉積物值(在較高溫度下更為明顯)可能源于它們略微更好的密度和不同的微觀結(jié)構(gòu)拓?fù)洌ㄔ诘?.2.1節(jié)中討論)。還可以觀察到,粗粉沉積物表現(xiàn)出比細(xì)粉沉積物略高的導(dǎo)熱率,這在兩種工藝參數(shù)下都是相似的趨勢(shì)。這可能再次是由特定的微觀結(jié)構(gòu)拓?fù)湟鸬?。?duì)于所有樣品,導(dǎo)熱率隨著溫度升高而降低。在金屬中,這是一種眾所周知的現(xiàn)象,因?yàn)樗鼈兊膶?dǎo)熱率主要取決于電子的流動(dòng),而電子的流動(dòng)受到升高溫度下晶格振動(dòng)的阻礙 [24, 25]。 圖5顯示了具有代表性的應(yīng)力-應(yīng)變曲線。這些結(jié)果表明,在低壓 (LP) 下,兩種冷噴涂沉積物都表現(xiàn)出高抗拉強(qiáng)度,但延展性非常低。這些特性是沉積態(tài) CSAM材料的典型特征,并且是粉末顆粒塑性變形過程中極端加工硬化的結(jié)果。改變游戲規(guī)則的結(jié)果是在高壓 (HP) 下沉積的Cu樣品的曲線。這些曲線的特點(diǎn)是高抗拉強(qiáng)度和高延展性,兩者都與塊狀(即非增材制造)對(duì)應(yīng)物完全相當(dāng)。開發(fā)一種同時(shí)具有高強(qiáng)度和高延展性的增材制造材料一直是一項(xiàng)具有挑戰(zhàn)性的任務(wù),特別是自從強(qiáng)度和延展性通常是相互排斥的。據(jù)我們所知,以前沒有報(bào)道過冷噴涂銅在噴涂狀態(tài)下能取得這樣的結(jié)果。 拉伸測試數(shù)據(jù)進(jìn)一步表明,使用較細(xì)粉末在兩種工藝參數(shù)下噴涂的銅涂層,與使用較粗原料粉末噴涂的銅涂層相比,顯示出更高的強(qiáng)度。然而,這種影響不如工藝參數(shù)的影響顯著。 將晶粒從粗晶細(xì)化到超細(xì)晶,再到納米級(jí)晶粒,是強(qiáng)化金屬材料的一種眾所周知的方法[26, 27]。這種方法的代價(jià)通常是延展性較差,因?yàn)閮?chǔ)存位錯(cuò)的能力有限,導(dǎo)致在機(jī)械加載過程中早期發(fā)生應(yīng)變局部化。為了克服這個(gè)問題,制造雙峰晶粒尺寸的微觀結(jié)構(gòu)已被證明是一種在超細(xì)晶材料中提高延展性的策略,但會(huì)略微犧牲拉伸強(qiáng)度。在具有這種雙峰晶粒尺寸分布的材料中,超細(xì)晶提供高強(qiáng)度,而粗晶則作為位錯(cuò)存儲(chǔ)的“阱”,從而提高延展性[28-31]。拉伸測試數(shù)據(jù)表明,在高功率(HP)條件下,銅涂層可能具有這種雙峰微觀結(jié)構(gòu),使其具有高強(qiáng)度和延展性。為了研究這一假設(shè),并檢測潛在的微觀結(jié)構(gòu)再結(jié)晶,我們獲取了所有四個(gè)冷噴涂增材制造(CSAM)涂層的電子背散射衍射(EBSD)反極圖(IPF)和局部晶粒取向差(KAM)圖。 圖 66 中所示的反極圖(IPF)清楚地顯示了一種特定的微觀結(jié)構(gòu),其中位于原始銅顆粒中心的粗晶區(qū)域被沿顆粒邊緣的幾微米大小的超細(xì)晶的連續(xù)網(wǎng)絡(luò)所包圍。細(xì)粉-低功率(Fine-LP,顆粒速度 688 米/秒)和細(xì)粉-高功率(Fine-HP,顆粒速度 813 米/秒)涂層的反極圖顯示,在兩種工藝參數(shù)下都形成了清晰可見的雙峰結(jié)構(gòu)。然而,在低功率(LP)條件下,粗晶和細(xì)晶的空間拓?fù)浞植疾⒉痪鶆?,一些區(qū)域只顯示細(xì)晶,并且超細(xì)晶網(wǎng)絡(luò)的分布也進(jìn)一步不均勻。與低功率(LP)條件相反,細(xì)粉-高功率(Fine-HP)涂層的微觀結(jié)構(gòu)顯示出粗晶和細(xì)晶均勻的空間拓?fù)浞植迹渲写志^(qū)域有規(guī)則地被相互連接的超細(xì)晶網(wǎng)絡(luò)所環(huán)繞。正如其他研究(例如,Zhang 等人對(duì) 304L 不銹鋼的研究 [32])所發(fā)現(xiàn)的,空間拓?fù)浞植迹ㄟ@里討論的是我們的涂層)是在高功率(HP)條件下同時(shí)實(shí)現(xiàn)高延展性和高強(qiáng)度的另一個(gè)主要因素。在低功率(LP)和高功率(HP)條件下,粗銅粉末涂層的微觀結(jié)構(gòu)也觀察到類似的行為:粗粉-低功率(Coarse-LP,顆粒速度591米/秒)的微觀結(jié)構(gòu)顯示出分布不均勻的細(xì)長的大晶粒,以及不規(guī)則且相對(duì)較厚的超細(xì)晶網(wǎng)絡(luò),而粗粉-高功率(Coarse-HP,顆粒速度662米/秒)則顯示出更均勻分布的粗晶區(qū)域,這些區(qū)域被相對(duì)較薄的超細(xì)晶壁所環(huán)繞。在所有涂層中,微觀結(jié)構(gòu)中觀察到的細(xì)長粗晶的出現(xiàn)可能是由于粉末顆粒撞擊期間的射流現(xiàn)象造成的,正如 Borchers 等人 [33] 和 Rahmati 等人 [34] 所報(bào)告的那樣。 從電子背散射衍射(EBSD)結(jié)果可以清楚地看出,所有四個(gè)涂層都表現(xiàn)出雙峰結(jié)構(gòu),但它們的細(xì)晶和粗晶比例不同。為了量化這種差異,我們使用EBSD反極圖(IPF)來計(jì)算每個(gè)涂層內(nèi)的面積加權(quán)晶粒尺寸分布(圖7)。直方圖清楚地表明,工藝參數(shù)(低功率LP與高功率HP)對(duì)晶粒尺寸分布產(chǎn)生顯著影響。對(duì)于兩種類型的原料粉末,在高功率HP下噴涂的涂層顯示出更大比例的較大晶粒。這種轉(zhuǎn)變是由前文討論的晶粒再結(jié)晶引發(fā)的,并產(chǎn)生一種由細(xì)晶和粗晶組成的微觀結(jié)構(gòu)。就絕對(duì)值而言,細(xì)粉和粗粉的中值晶粒尺寸分別從2.3微米變?yōu)?.9微米,以及從 3.1微米變?yōu)?.8微米。此外,與工藝參數(shù)的影響不同,在低功率LP和高功率HP 下,兩種粉末之間沒有顯著差異。 為了進(jìn)一步了解微觀結(jié)構(gòu)的形成,我們從反極圖(IPF)中計(jì)算了局部晶粒取向差(KAM)圖,揭示了涂層中的塑性應(yīng)變程度(圖 8)。結(jié)果表明,在低功率(LP)下噴涂的兩種涂層都表現(xiàn)出粗晶內(nèi)部以及晶界處的高度應(yīng)變。還可以觀察到,未指數(shù)化區(qū)域(主要限于顆粒邊界和粗晶-細(xì)晶界面區(qū)域)的比例在細(xì)粉-低功率(Fine-LP)中更高,表明要么是具有高位錯(cuò)密度的高度變形區(qū)域,要么是小于電子背散射衍射(EBSD)分辨率限制的非常小的納米晶特征。與低功率(LP)的圖相比,兩種高功率(HP)涂層的取向差圖顯示出應(yīng)變較小的區(qū)域,并且?guī)缀鯖]有未指數(shù)化的區(qū)域。 總而言之,電子背散射衍射 (EBSD) 結(jié)果表明,雖然塑性應(yīng)變?nèi)匀淮嬖冢珶彳浕驮俳Y(jié)晶在粒子極高沖擊速度造成的剪切應(yīng)變中占主導(dǎo)地位。文獻(xiàn)中也有報(bào)道,對(duì)于銅而言,超過600米/秒的顆粒速度足以將局部溫度升高到接近熔點(diǎn),即足以在高度應(yīng)變的材料中發(fā)生動(dòng)態(tài)再結(jié)晶 [33-35]。在本研究中,在低功率 (LP) 和高功率 (HP) 下獲得的顆粒速度足以觸發(fā)兩種粉末的這一過程。 在之前的研究{例如,[33]}中,有人提出在高應(yīng)變速率變形的動(dòng)態(tài)再結(jié)晶過程中,微觀結(jié)構(gòu)的演變分為五個(gè)階段:(i) 位錯(cuò)的隨機(jī)分布,(ii) 通過形成細(xì)長的位錯(cuò)胞進(jìn)行動(dòng)態(tài)回復(fù),(iii) 細(xì)長的位錯(cuò)胞排列形成細(xì)長的亞晶粒,(iv) 細(xì)長的亞晶粒的分解,以及 (v) 形成具有小等軸晶粒的再結(jié)晶微觀結(jié)構(gòu)。正如Borchers 等人 (2003) 和Schmidt 等人 (2006) 所報(bào)告的那樣,更高的顆粒速度會(huì)產(chǎn)生更高的局部溫度升高,從而為微觀結(jié)構(gòu)的演變提供更多時(shí)間 [33, 36]。 本研究的結(jié)果表明,在低功率(LP)條件下,高溫條件存在的時(shí)間不足,因此,再結(jié)晶無法充分發(fā)展。相反,微觀結(jié)構(gòu)的發(fā)展在早期階段停止,因此,形成了觀察到的高度應(yīng)變和非均質(zhì)的雙峰微觀結(jié)構(gòu)。這影響了冷噴涂增材制造(CSAM)銅涂層的力學(xué)性能,表現(xiàn)出高強(qiáng)度但非常低的延展性。與此相反,在高功率(HP)下,兩種粉末的更高顆粒速度會(huì)誘導(dǎo)更高的溫度,從而促進(jìn)動(dòng)態(tài)再結(jié)晶并刺激完全發(fā)展的具有松弛晶粒的雙峰微觀結(jié)構(gòu)。結(jié)果進(jìn)一步表明,需要均勻且松弛的雙峰微觀結(jié)構(gòu),其中粗晶區(qū)域被超細(xì)晶的連續(xù)網(wǎng)絡(luò)所環(huán)繞,才能獲得同時(shí)實(shí)現(xiàn)高強(qiáng)度和高延展性的協(xié)同效應(yīng)。在本研究中,對(duì)于在高功率(HP)下噴涂的兩種粉末都觀察到了這一點(diǎn)。Jakupi 等人 (2015) [35] 此前也報(bào)道了冷噴涂銅中的雙峰微觀結(jié)構(gòu)。然而,那里展示的雙峰結(jié)構(gòu)在粗晶區(qū)域和超細(xì)晶網(wǎng)絡(luò)的空間拓?fù)浞植贾斜憩F(xiàn)出異質(zhì)性,因此,觀察到的高強(qiáng)度伴隨著非常低的延展性,這與我們?cè)诘凸β剩↙P)下的結(jié)果相似。 圖9展示了粉末粒度和工藝參數(shù)對(duì)冷噴涂增材制造(CSAM)銅涂層硬度的影響。硬度趨勢(shì)與拉伸強(qiáng)度行為趨勢(shì)一致(圖5),即細(xì)粉涂層由于其更細(xì)的晶粒結(jié)構(gòu)(如圖6所示)而顯示出更高的硬度值。細(xì)晶微觀結(jié)構(gòu)包含高密度的晶界,這些晶界充當(dāng)位錯(cuò)運(yùn)動(dòng)的障礙,導(dǎo)致壓痕期間位錯(cuò)在靠近晶界的區(qū)域堆積。因此,需要更高的應(yīng)力才能使位錯(cuò)通過這些堆積,從而導(dǎo)致硬度增加[37]。 然而,在所使用的工藝參數(shù)下,細(xì)粉和粗粉涂層的硬度值差異并不是非常顯著。與此相反,工藝參數(shù)的影響得到了很好的體現(xiàn)。通過雙尾t檢驗(yàn)進(jìn)行的統(tǒng)計(jì)分析表明,在低功率(LP)和高功率(HP)下沉積的樣品的硬度平均值之間存在顯著差異(p<0.01)。顯然,正如第3.2.1節(jié)中所討論的那樣,在低功率(LP)下,剪切應(yīng)變?cè)谠俳Y(jié)晶中占主導(dǎo)地位,而在高功率(HP)下,獲得了完全再結(jié)晶和松弛的微觀結(jié)構(gòu)。因此,兩種高功率(HP)涂層的硬度均降低。非常低的標(biāo)準(zhǔn)偏差表明,所有四個(gè)冷噴涂增材制造(CSAM)銅涂層在宏觀性能方面都非常均勻。*后,冷噴涂銅涂層的硬度與塊體銅相當(dāng)。 使用球形粉末、高壓槍和氮?dú)庾鳛楣に嚉怏w,制造出了純銅的冷噴涂增材制造(CSAM)涂層。研究了工藝參數(shù)和粉末粒度的影響。從結(jié)果中可以得出以下結(jié)論: 幾乎無孔的銅涂層(密度為 8.79–8.84 g/cm3,完全抑制氦氣泄漏)可以通過冷噴涂增材制造(CSAM)生產(chǎn),其熱導(dǎo)率高達(dá) 368 W/m?K,與原始噴涂狀態(tài)下的塊體銅(396 W/m?K)相當(dāng)。 在沒有任何二次加工(如熱處理)的情況下,無論使用何種銅粉,在高噴涂參數(shù)下,涂層都可以實(shí)現(xiàn)同時(shí)具有高強(qiáng)度和高延展性。這得益于雙峰微觀結(jié)構(gòu)的有利拓?fù)浣Y(jié)構(gòu),該結(jié)構(gòu)由粗晶組成,這些粗晶被沿單個(gè)顆粒邊緣的細(xì)晶網(wǎng)絡(luò)所包圍。 工藝氣體參數(shù)(溫度和壓力)對(duì)力學(xué)性能的影響比所用原料的平均粒徑更為顯著。在冷噴涂增材制造(CSAM)銅中實(shí)現(xiàn)了286MPa 的極限抗拉強(qiáng)度和24%的延展性的組合。 在我們的工作中開發(fā)的冷噴涂增材制造(CSAM)銅涂層的熱力學(xué)性能與采用非增材冶金方法生產(chǎn)的塊體銅完全相當(dāng)??紤]到高沉積效率(99%)和高沉積速率,本文說明了該方法在各個(gè)工業(yè)領(lǐng)域中具有巨大的應(yīng)用潛力,無論是在高要求的應(yīng)用中還是在批量生產(chǎn)中。注:此文獻(xiàn)由deepseek翻譯,如有不妥之處,歡迎指正!